When I first learned about the US patent application horizontal self burrowing robots, I was fascinated by their potential to revolutionize how we approach underground construction and environmental projects.
The US patent application horizontal self burrowing robots refers to innovative machines designed to dig underground tunnels autonomously, minimizing surface disruption. These robots leverage advanced sensors and AI for efficient navigation through various soil types.
Stay tuned with us as we explore the horizontal self burrowing robot us patent! We’ll discuss its innovative features and potential impact on various industries.
What Is A Horizontal Self-Burrowing Robot?
A horizontal self burrowing robot us patent is an autonomous machine designed to excavate underground tunnels without disrupting the surface. These robots employ advanced sensors and artificial intelligence (AI) to navigate and burrow through various soil and rock conditions, offering a sustainable alternative to traditional excavation methods.
The Need for Horizontal Self-Burrowing Robots:
Conventional excavation techniques such as trenching and drilling can be labor-intensive, costly, and environmentally damaging. The us patent bioinspired horizontal self burrowing robot addresses these challenges by providing a solution that minimizes surface disturbance, reduces labor costs, and enhances safety in excavation projects.
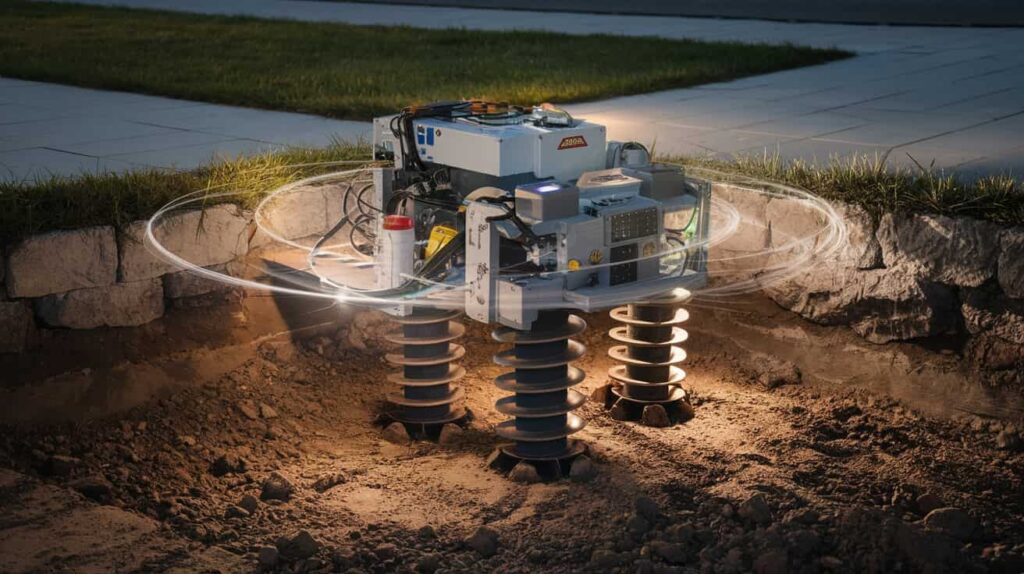
Key Benefits Of Horizontal Self Burrowing Robots:
- Cost Efficiency: Automating the excavation process reduces labor costs and the need for heavy machinery.
- Minimized Surface Disruption: These robots operate underground, preserving the surface environment and reducing the need for extensive land restoration.
- Enhanced Safety: Removing human workers from hazardous underground environments significantly lowers the risk of accidents and injuries.
- Increased Precision: These robots can navigate complex underground conditions with high accuracy, allowing for precise tunneling and minimizing the risk of damaging existing infrastructure or utilities.
- Environmental Sustainability: By reducing the need for extensive land clearing and heavy machinery, the US patent bioinspired horizontal self burrowing robot contributes to a smaller carbon footprint, making it a more eco-friendly option for excavation and construction projects.
Core Features Of Horizontal Self-Burrowing Robots – Let’s See!
Autonomous Navigation:
horizontal self burrowing robot us patent have sophisticated navigation systems that allow them to operate independently. These systems use real-time data from various sensors to adapt their paths, avoiding obstacles such as rocks, roots, and existing underground utilities.
Burrowing Mechanism:
The burrowing mechanism of these robots is engineered for versatility and efficiency. Employing rotating drill heads or cutting tools, these robots can operate across various soil and rock types. This adaptability is crucial for successful operations in different environments.
Sensor Systems for Obstacle Detection:
Advanced sensor technologies, including infrared, sonar, and LIDAR, enable horizontal self-burrowing robots to detect and navigate around obstacles. These sensors work together to create a detailed map of the surrounding underground environment, allowing the robots to make informed decisions during excavation.
Power Source Options:
Various energy sources, including hydraulic systems, electric batteries, or renewable energy like solar power, can power horizontal self-burrowing robots. This flexibility allows them to operate efficiently in remote locations and contributes to sustainability efforts.
Data Collection And Reporting:
These robots are equipped with data collection capabilities to gather information about soil conditions, environmental factors, and excavation progress. This data can be analyzed to improve future operations and provide valuable insights for engineers and project managers.
How Do Horizontal Self-Burrowing Robots Operate?
- Planning and Path Selection: Before excavation, the robot’s onboard computer analyzes pre-programmed routes based on project needs. This planning helps determine the most efficient path while avoiding known obstacles.
- Autonomous Navigation: These robots use advanced navigation systems that rely on real-time data from sensors like GPS and LIDAR. This allows them to adjust their paths dynamically to avoid unexpected operational obstacles.
- Burrowing Mechanism Activation: Once in motion, the robot activates its burrowing mechanism, which includes rotating drill heads or cutting tools. This design is engineered for energy efficiency and enables consistent operation across different soil types.
- Sensor Integration for Obstacle Detection: The robot’s advanced sensors continuously scan the underground environment to create a detailed map. Technologies like infrared and sonar help identify obstacles and changes in soil conditions.
- Data Collection and Analysis: The robot gathers data on soil type, moisture levels, and potential hazards during excavation. This information aids operators and improves future project efficiency.
- Power Management: Horizontal self-burrowing robots can operate on various power sources, including hydraulic systems or rechargeable batteries. Some models may utilize renewable energy sources, such as solar power, for enhanced sustainability.
- Completion and Reporting: After reaching its endpoint, the robot can either return to its starting point or transition to a new task. It provides detailed reports on excavation progress, including encountered obstacles and collected data.
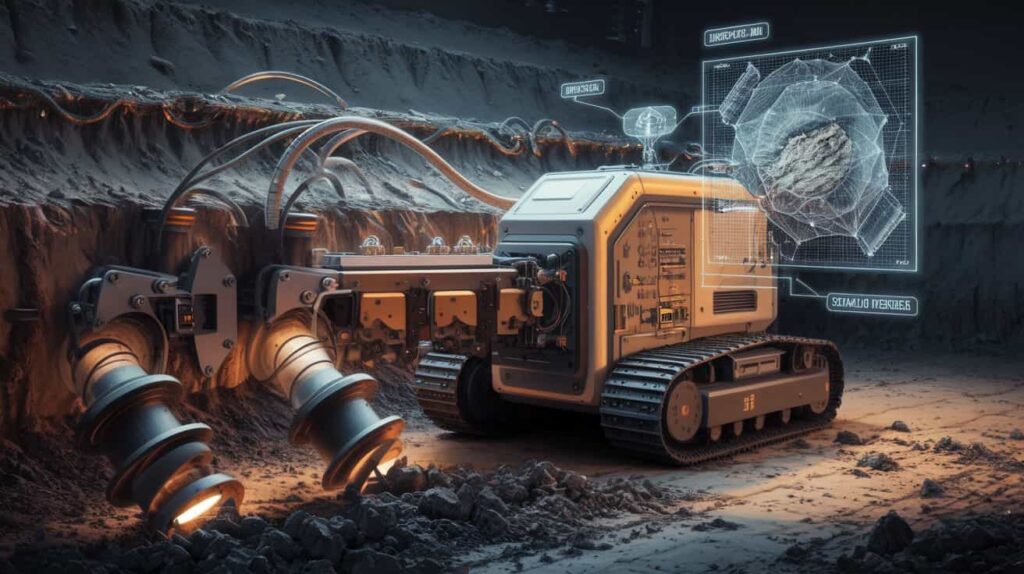
Potential Applications Of Horizontal Self-Burrowing Robots – You Must Read!
The versatility of us patent bioinspired horizontal self burrowing robot opens up various applications across various industries.
Construction And Civil Engineering:
In construction, these robots can facilitate tunneling for essential infrastructure projects, including pipelines, roadways, and rail systems. Their ability to operate with minimal surface disturbance is particularly valuable in urban environments where space is limited.
Utility Installation And Maintenance:
Horizontal self-burrowing robots are ideal for installing and maintaining underground utilities, such as fiber-optic lines and water pipes. By reducing the need for extensive excavation, these robots help minimize public disruption and environmental impact.
Environmental Monitoring And Remediation:
In environmental science, self-burrowing robots can help collect soil samples, monitor conditions, and aid in pollution remediation efforts. Their capacity to navigate hazardous or inaccessible areas makes them invaluable for environmental research.
Mining And Resource Extraction:
The mining industry stands to benefit significantly from the implementation of horizontal self-burrowing robots. By creating smaller, more precise tunnels, these robots can enhance the efficiency of resource extraction while minimizing material disturbance.
What Challenges Do These Robots Face During Operation?
Complex Underground Conditions:
The underground environment can vary greatly, with different soil types, rocks, and debris hindering the robot’s progress and requiring adjustments in its burrowing technique. This unpredictability can lead to delays and increased operational costs.
Accurate Navigation:
Ensuring precise navigation is tricky. The robot must constantly adapt its path based on real-time data, which can be affected by unexpected obstacles or changes in the underground landscape. Any inaccuracies in navigation can result in inefficient tunneling and potential damage to existing infrastructure.
Sensor Limitations:
While advanced sensors help detect obstacles, they can sometimes struggle in extremely challenging conditions, such as very dense soil or areas with a lot of interference, leading to potential navigation errors. The excavation process can be jeopardized if sensors fail or provide inaccurate readings.
Power Supply Issues:
Maintaining a consistent power supply can be challenging, especially in remote locations. The robot must have enough energy to complete its tasks midway without running out of power. Limited access to charging facilities can further complicate operations and planning.
Maintenance And Repair:
Operating underground can wear out the robot’s components. Regular maintenance and the ability to perform repairs in the field are essential to keeping the robots functioning optimally. Lack of immediate access to spare parts can lead to extended downtime and project delays.
How Does The US Patent Application Process Work For Horizontal Self-Burrowing Robots?
- Preparation of Patent Application: Inventors must create a detailed application that describes the horizontal self burrowing robot us patent design and functionality. This document should include drawings that clearly illustrate the invention.
- Filing the Application: The application is filed with the United States Patent and Trademark Office (USPTO) electronically or by mail. Inventors must also pay the necessary filing fees, which vary by patent type.
- Patent Examination: A patent examiner reviews the application to determine whether the invention is novel, non-obvious, and useful. Depending on the complexity and backlog, this examination process can take several months to years.
- Office Actions and Responses: The examiner may issue an Office Action with rejections or requests for additional information. Inventors can respond by addressing concerns or amending the application.
- Approval or Rejection: If the invention meets patentability requirements, the USPTO grants the patent, and the inventor receives a certificate. If rejected, inventors can appeal or modify the resubmission application.
- Patent Maintenance: After a patent is granted, inventors must pay maintenance fees regularly to keep it active. Failure to pay these fees can result in the patent’s lapsing and loss of exclusive rights.
- Enforcement of Patent Rights: Once a patent is obtained, the inventor has exclusive rights to manufacture and sell the robot. This includes the ability to enforce the patent against unauthorized use or infringement.
How Will Horizontal Self-Burrowing Robots Impact The Market?
Horizontal self-burrowing robots are set to transform industries that rely on underground excavation, such as construction, mining, and utilities. By automating the digging process, these robots can significantly lower labor costs and reduce the need for heavy machinery, making projects more affordable.
Additionally, their ability to work underground means less disruption to the surface environment, which is increasingly important in urban areas. This combination of cost savings and environmental benefits makes these robots attractive for businesses looking to improve efficiency and sustainability in their operations.
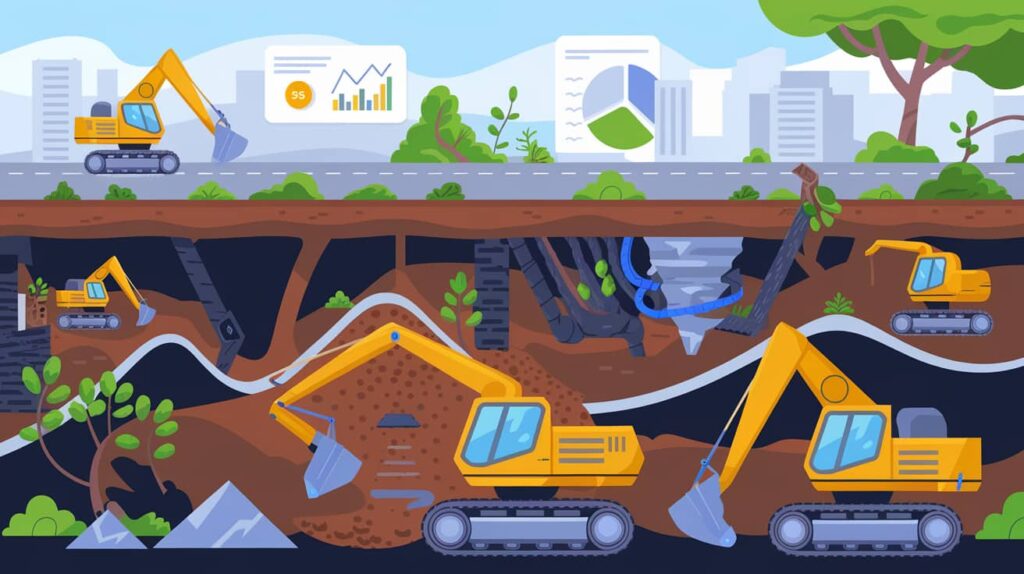
How Can Collaborations Enhance Adoption Of Horizontal Self-Burrowing Robots?
Collaborations can greatly speed up the adoption of horizontal self-burrowing robots by bringing together different experts and resources. When innovators partner with research institutions, they can gain valuable insights and improve the technology. Working with utility and construction firms allows for practical testing, showing how these robots can be used in real-world projects.
Additionally, teaming up with government agencies can provide funding and help navigate regulations. These partnerships build trust and create a supportive environment that encourages innovation, making it easier for businesses to adopt this new technology.
What Future Innovations and Upgrades Can We Expect for Horizontal Self-Burrowing Robots?
The future of horizontal self-burrowing robots holds exciting potential for innovations and upgrades to enhance their capabilities. Advances in artificial intelligence (AI) will allow these robots to navigate even more complex underground environments with greater precision. Improved sensor technologies could lead to better obstacle detection, allowing the robots to avoid potential hazards and adapt in real-time to changing conditions.
Furthermore, developing stronger, lighter materials will enhance durability and reduce energy consumption, making the robots more efficient. Integrating renewable energy sources, such as solar power, can make operations more sustainable. Overall, these innovations will drive the effectiveness and reliability of horizontal self-burrowing robots, expanding their applications across various industries.
Frequently Asked Questions:
How do these robots improve safety in excavation?
By automating the excavation process, horizontal self-burrowing robots keep human workers out of potentially dangerous underground environments. This significantly reduces the risks of cave-ins, equipment failures, and other hazards, contributing to safer construction and mining operations.
Can these robots operate in different soil and rock conditions?
Yes, horizontal self-burrowing robots are designed to function across various soil and rock types. Their burrowing mechanisms can adjust to the density and composition of the materials they encounter. This versatility is crucial for successful operation in diverse environments, from urban to remote areas.
How do horizontal self-burrowing robots reduce labor costs?
By automating the excavation process, these robots significantly decrease the need for large labor teams and heavy machinery. This results in lower operational costs for construction and mining projects. Additionally, the reduced time required for excavation can lead to quicker project completion.
What types of sensors do these robots use?
Horizontal self-burrowing robots utilize various sensors for obstacle detection and navigation, including infrared, sonar, and LIDAR. These sensors work together to create a detailed map of the underground environment. Their advanced technology allows for precise and efficient burrowing operations.
How can companies integrate these robots into their operations?
Companies can integrate horizontal self-burrowing robots by collaborating with technology developers and conducting pilot projects. Training personnel on the operation and maintenance of the robots is essential for successful implementation.
Conclusion:
Horizontal self-burrowing robots represent a significant advancement in subterranean excavation technology. These robots promise to revolutionize the construction, mining, and environmental science industries by automating the burrowing process.
With the potential to lower costs, improve safety, and reduce environmental impact, this technology is poised to become an essential tool for future subterranean exploration.
You Also Have To Check: